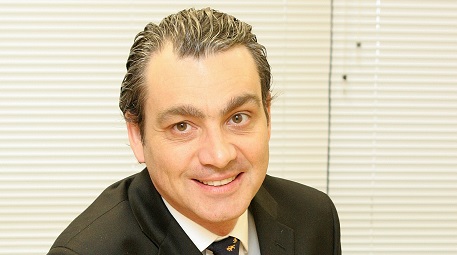
Although things have improved significantly in some regions of the United States, with automakers enjoying growth and profitability at pre-recession levels, global markets remain uneven. While North America had a robust outlook with a forecast of 16 million cars - up from 13 million in 2008 - the same strategy and analysis found that car sales in South America fell 15%, based on data from August 2014. Russian car sales fell by 25% in the same period.
The outlook in Europe is also quite weak, as the region emerges from six years of falling sales. And things are not much better in the Asia - Pacific region, with inconsistent performance in the Indian market and slow growth in China.
A cloud business management software (ERP) is the only one capable of dealing with the diverse needs and challenges of the global automotive industry. Cloud ERP systems can help free up capital by giving you the flexibility to meet your growing operational needs. Check out five reasons why using a cloud ERP can help the auto industry - and other sectors of the economy - face the crisis:
1. Cost reduction
Moving to the cloud can significantly reduce costs. A survey by Computer Economicsshows that organizations that have moved most or all of their systems to the cloud have seen an average of 15% reduction in IT expenses. This reduction comes not only from a reduction in expenses with the central database, but also with costs with the IT personnel sector.
In addition, cloud-based implementations require less resources for development and testing, with vendors generally providing the most application support and maintenance. As a result, companies that implement cloud applications spend 40% less on consulting and 25% less on staff support than companies that implement on-premise applications, according to a study by Nucleus Research.
Cloud solutions are typically more cost-effective than on-premise solutions. A study by Strategy &found that the total cost of having a cloud solution can be 50 to 60% less than for traditional solutions over a 10-year period.
By freeing themselves from capital expenditures that would be used for maintenance and implementation in on-premise solutions, companies have more money available to drive growth initiatives.
2. Accelerates performance
With the cloud, deployments are faster, there is less slowness during implementation, and there is no need to invest in infrastructure. According to Strategy &, cloud deployments can be up and running for 4 to 8 months, compared to 12 to 36 months for on-premise solutions. Because cloud deployments require less in-house support - both in terms of physical structure and human resources - companies experience little business disruption during the process.
3. Rapid growth
Cloud implementations help reduce costs and make it faster to establish a business unit or presence in new and remote places. If a business is successful, companies can scale the solution to meet expansion needs with agility. If the enterprise is offering less than expected results, a minimum investment in the cloud for that location represents a much smaller loss than the company would incur with an on-premise solution.
A cloud ERP solution is also much easier to update than on-premise solutions. This means that the solution will always be up-to-date and able to meet business needs, processes, regulations and requirements, as they evolve over time.
4. Improves efficiency
The growth of a business is only profitable if it is balanced with the growth of inventory turns, consolidated processes, efficiency gains and reduction of other operating costs. Cloud solutions are ideas for improving the efficiency of operations because they can help automate many of the typical steps in automotive business processes, replacing manual activities and virtually eliminating the need to duplicate data entry.
In the automotive industry, production operations are spread across a complex value chain made up of various original equipment suppliers and manufacturers (OEMs). Cloud ERP implementations can be the way to support a high degree of coordination and collaboration between OEMs and suppliers.
An enterprise-wide cloud ERP also extends early detection capabilities and real-time access to information on employee capacity, availability, skills and interdependencies, tools and data. As a result, manufacturers have access to the information needed to adjust programs and avoid potential disruptions.
5. Improves visibility
With complete visibility of the entire company system and with information on shop floor resources, manufacturers can use limited resources more effectively, find areas where they can increase throughput and efficiency, and provide better material and asset management . Being able to see how all the elements are interrelated and in real time, manufacturers can operate more efficiently and make better and faster decisions.
Companies also gain access to robust collaboration tools that span the entire company and suppliers. With this, you can discover potential problems, more quickly and accurately, analyze them more deeply, find their causes and identify solutions before they create bottlenecks.